Aluminium Billets
Aluminum Billet
Aluminum billets are semi-finished products made through casting shaped into cylindrical or rectangular forms. These billets are prized for their combination of low density, excellent corrosion resistance, good workability, and superior thermal and electrical properties, making them highly versatile in various industrial applications.
Applications of Aluminum Billet
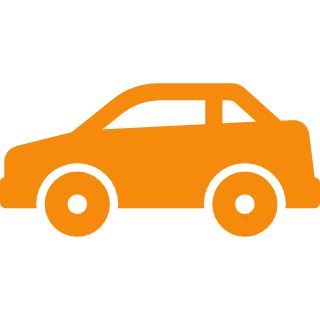
Automotive
For structural components and lightweight parts.
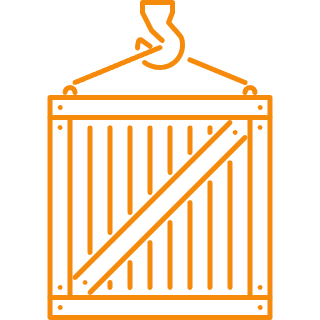
Transportation
Used in frames and structural components.
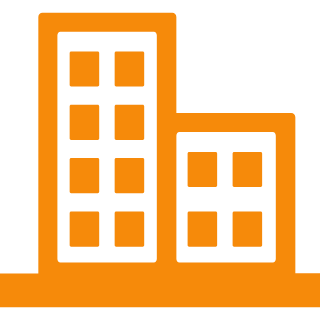
Building & Construction
For window frames, doors, and roofing materials.
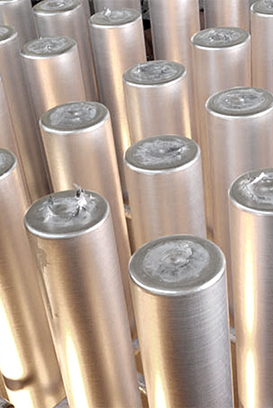
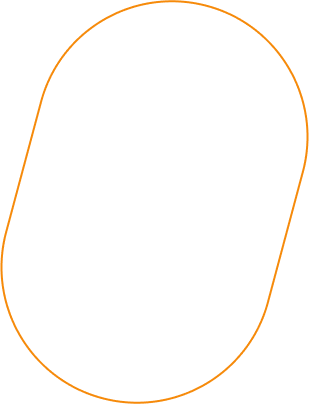
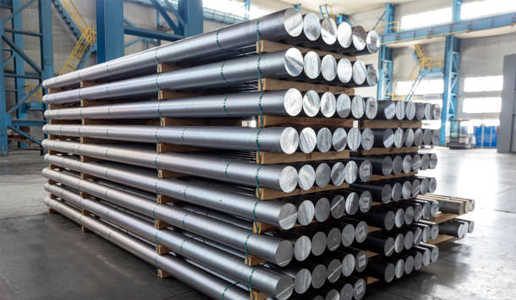
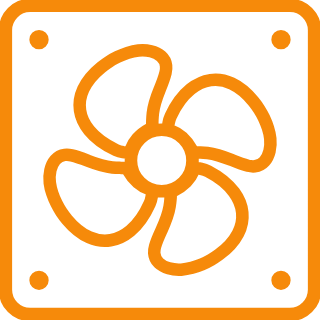
HVACR
In heat exchangers and other HVAC systems.
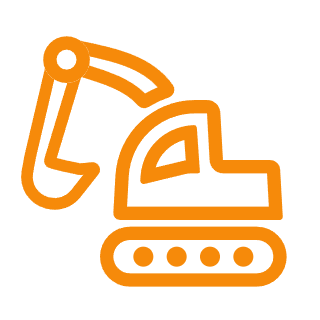
General Engineering
For custom parts and machinery components.

Electronics
In conductors, casings, and other components.
- High extrudability and excellent surface quality.
- Consistency in properties and high mechanical performance.
- Improved extrusion speed and process recovery, enhancing die life and overall production efficiency.
Types and Grades of Aluminum Billet
Aluminum billets come in different series, each with specific alloy compositions and properties tailored for various applications:-
Pure Aluminum
Billets (1000 Series):
High purity aluminum with excellent corrosion resistance and
electrical conductivity, used in electrical wiring and architectural
components.
- 1050: Commercially pure aluminum alloy.
- 1100: Soft, used in heat exchangers and appearance items.
-
Aluminum Alloy Billets:
Enhanced with alloying elements to improve strength, corrosion
resistance, and other properties.
- 3000 Series: Manganese alloys, commonly used in heat exchangers and sheet metal work.
- 5000 Series: Magnesium-based alloys with good corrosion resistance, used in marine and architectural applications.
- 6000 Series: Magnesium-silicon alloys, known for strength, weldability, and corrosion resistance. Commonly used in structural components, automotive parts, and frames.
- 6063: Popular for extrusion, widely used in architectural applications.
- 6082: Stronger than 6061, used in automotive and structural applications.
- 6061: Common in the transportation and machinery industries due to its strength and fatigue resistance.
- 7000 Series: Zinc-based alloys, known for high strength and machinability, commonly used in aerospace, automotive, and sporting goods.
- 7075: High strength, used in aerospace.
- 7004: High weld strength, used in aerospace applications.
Specialized Billets
- High-Strength Aluminum Billets: Used where high strength is essential, such as in structural applications.
- Heat-Treatable Aluminum Billets: Alloys like 5052 and 5083 offer good corrosion resistance and strength, often used in marine and transportation applications.
Manufacturing Process:
The manufacturing process of aluminum billets can be broken down into the following four primary steps:
- 01Selection of Raw
Materials
Aluminum billets are typically produced from aluminum scrap or primary aluminum. The choice of raw material is determined by factors such as cost, alloy composition, and material availability. The selected raw materials are essential for ensuring the final billet meets the desired mechanical and physical properties. - 02Melting and Alloying
The raw materials are then melted in a furnace, where the aluminum is heated to temperatures above its melting point (660°C or 1220°F). During this stage, alloying elements like copper, magnesium, silicon, or zinc are added to the molten aluminum to achieve specific material properties required for the intended application. - 03Billet Casting
There are two main methods of forming aluminum billets:- Casting: In this process, molten aluminum is poured into molds designed to the desired shape of the billet. Once the aluminum cools and solidifies, it takes the form of the mold.
- Extrusion: In extrusion, the heated aluminum is forced through a specially designed die. The die shape determines the billet's final shape, and high pressure from the extrusion press forces the material through the die.
- 04 Cooling
After the billet is formed, it must be cooled to ensure proper solidification. Cooling is a crucial step in achieving the desired metallurgical properties and structural integrity of the billet. Cooling can be done via air cooling or water quenching, depending on the specific alloy and its requirements. The cooling rate is carefully controlled to prevent defects and ensure uniform solidification.
These four steps ensure that aluminum billets meet stringent quality and performance standards for a wide range of industrial applications.