Infrastructure
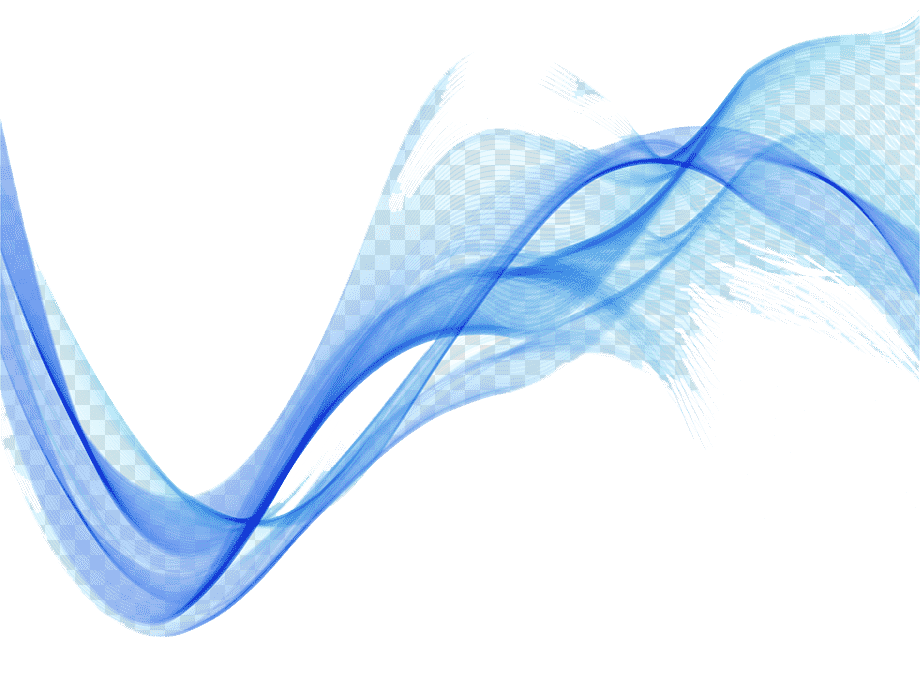
__ || BUILDING BRIDGES, BREAKING BARRIERS || __
Infrastructure
At VRK AlumartPvt. Ltd., our technology-focused approach has been
a key driver of our growth and success in the aluminum extrusion
industry. We understand that in a competitive market, staying
ahead of technological advancements is crucial for maintaining
product quality, efficiency, and customer satisfaction.
This commitment to continual technical upgradation is deeply
embedded
in the VRK Green way of working, where we continuously strive to
innovate and improve every aspect of our operations.
Foundary:
- 2 Castable melting furnaces with 10 ton capacity each with automated fluxing and nitrogen degassing machine with casting of billets with diameter 5″, 6″ and 7″
- Filtering the molten metal through CFF(ceramic double filteration system)to achieve a high degree of perfect superior alloy.
- Automatic temperature control advance system to monitor and regulate the furnace’s heating elements to ensure that the aluminum reaches and maintains the desired melting temperature.
- Specializedwater Cooling channelwith huge tanks holding up to 400,000 liters of waterwith controlled uniform flow of cool water used to control the cooling rate of the aluminum and ensure uniform solidification throughout the billet.
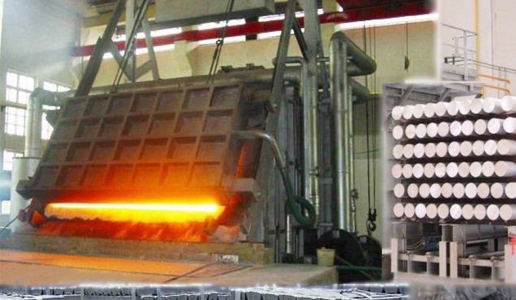
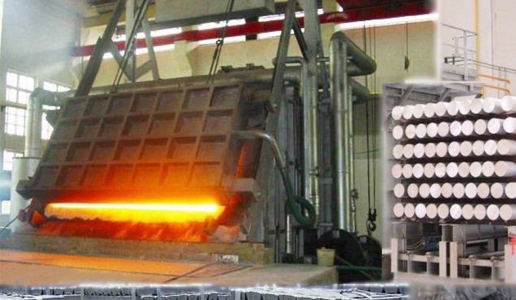
- Advanced Hot-Top Casting Technique
- Dross processing machine to efficiently remove unwanted dross (a byproduct of aluminum melting) from the molten metal. This ensures that the final product is free from impurities and maintains a high level of purity and consistency.
- Our system has CERTIFIED REFERENCE MATERIALS (CRM) for different alloys Certified by as per ISO 17034 for the use of validation of methods and calibration
- We are very soon coming up with CONTINOUS HOMOGENIZING SYSTEM (for best quality with perfect composition). The improved heat transfer results in shorter heat-up times for both small and large diameter billets.Homogenizing furnace lowers labour cost, uniform all billets with best log straightness.
- We are also coming up with Regenerative Burnersthat use a heat storage system to recover and reuse waste heat.
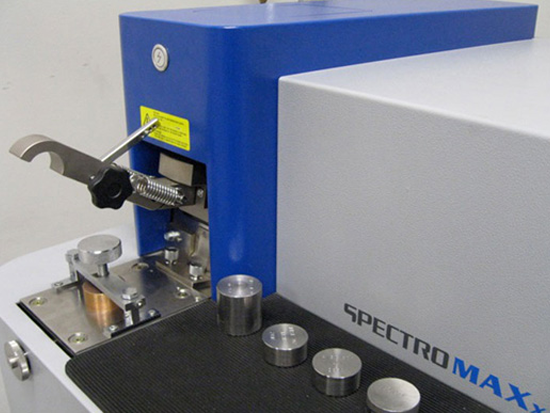
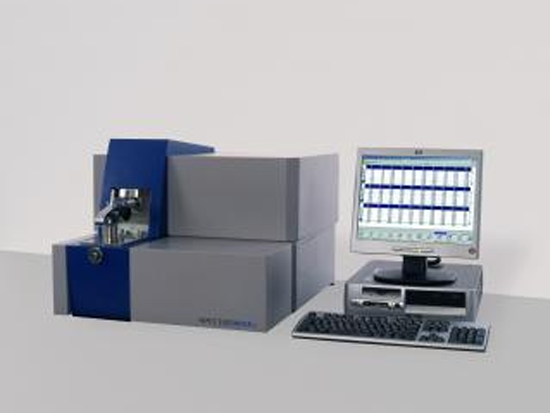
German-made Spectro Analytical Instrument(Spectromax):
- To maintain stringent quality standards, we employ German-made Spectro Analytical Instrument (SPECTROMAX) for automated and precise monitoring to check composition of materials like Manganese (Mn), Iron (Fe), Magnesium (Mg), Silicon (Si), Zinc (Zn), Titanium (Ti), Chromium (Cr), Copper (Cu), and Aluminium (Al)
In-House CAD Drawings:
- With our In-House CAD Drawing Services, VRK AlumartPvt. Ltd. ensures that every aluminum extrusion product is meticulously designed to meet your exact requirements. Whether you provide a PDF specification, a physical sample, or require assistance with your design, our skilled engineers will work with you to create precise CAD drawings that are the foundation for producing high-quality, custom aluminum products. This service reflects our commitment to precision, collaboration, and customer satisfaction.
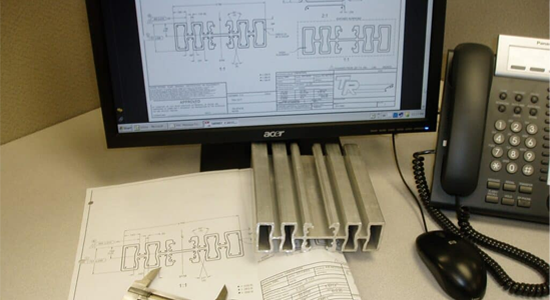
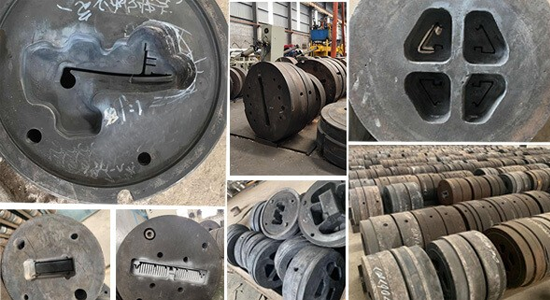
In-House Die Manufacturing:
- At VRK AlumartPvt. Ltd., our In-House Die Manufacturing capabilities allow us to deliver precision-engineered aluminum extrusion dies that meet the most intricate design requirements. By combining state-of-the-art technology, high-quality steel, and automated machinery, we ensure that each die is made to perfection, with a flawless finish and exceptional durability.
State of The Art Manufacturing Presses:
- 2 Extrusion presses, measuring 5”(1100Ton) and 6“(1600Ton), with capacity of 800MT monthly equipped with a cutting-edge fully automated PLC control system and a three head puller for producing twist and bend-free profilesto lessen man power for stainfree finished goods.
- An auto-conveyor belt handling system, a variable tonnage stretching machine paired with an auto-finish saw machine, further enhancing efficiency and accuracy.
- All presses have close controls on the speed and a high degree of stability. They are supported by Hot Log Shear , automatic puller and handling systems, producing extrusions which are bent and twist-free.
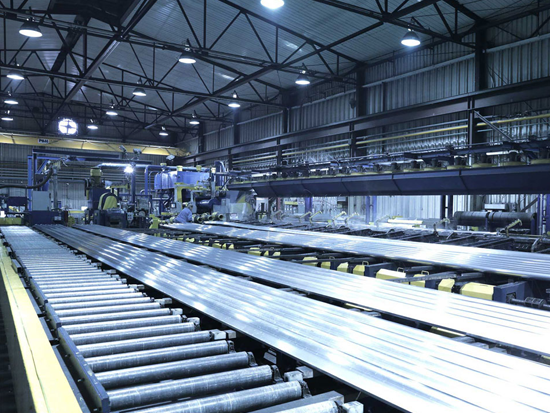
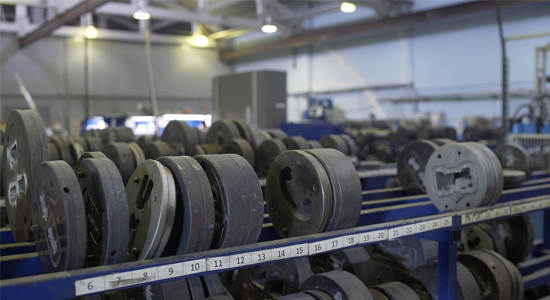
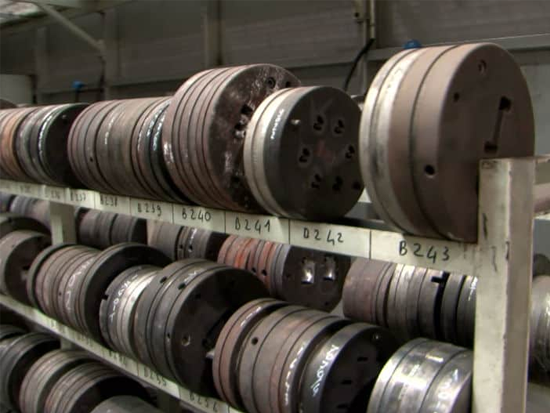
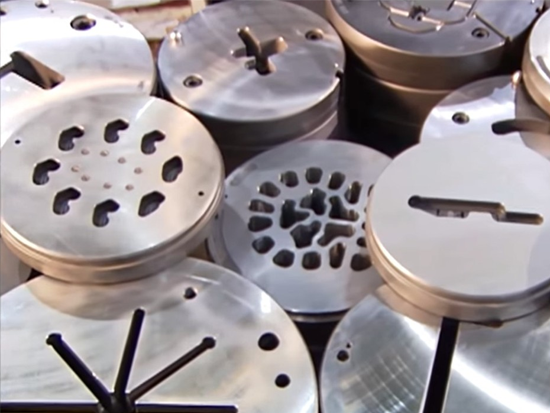
Tool Room:
The high demands placed on aluminum extrusion dies—particularly the high temperatures, friction, and deformation they endure—necessitate effective surface hardening techniques. At VRK AlumartPvt. Ltd., we implement advanced surface hardening processes to protect our dies from wear, improve their performance, and extend their service life.
- 3 Nitriding machines with a well-accepted surface hardening method against surface wear and deformation.
- 2 universal Lathe machine.
- Universal Milling machine.
- EDM(Electrical discharge machining).
- High precision Surface and profile Grinder.
- Bend Hexa.
Quality Control Testing Equipments:
- Computerized Spectrometerfor Metal Analysis.
- Straightness and Flatness Checking Surface Table.
- Universal Bevel Protector for Degree Checking.
- Precession Measuring Equipments Inspection at Various Levels
- Webster Hardness Tester
- UTM(Univeral Testing Machine) to test for both tensile and compressive strength
- Electrical Conductivity Meter
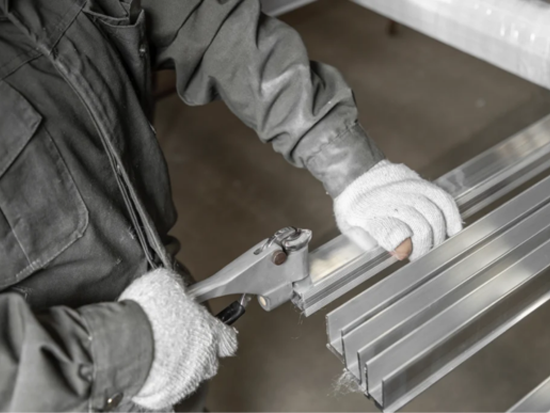
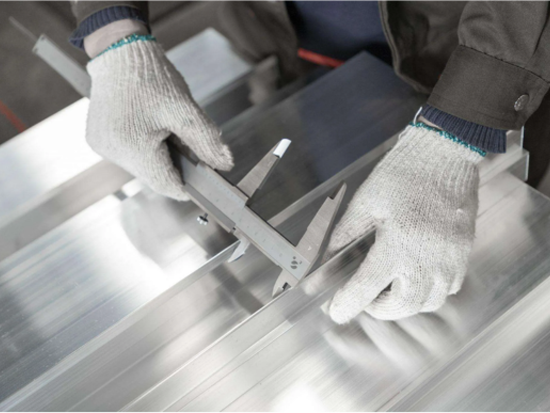
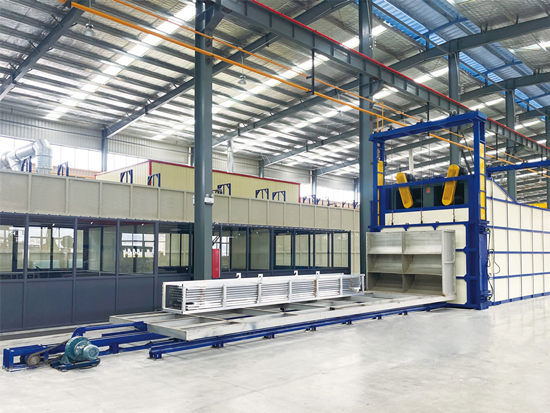
Aging:
The aging process involves subjecting the extruded profiles to
controlled heat and holding them at a specific temperature for a
set periodto improve the mechanical properties of aluminum
extrusions,increasing their strength and durability.
The two common tempers, T5 and T6, are achieved through
different aging processes.
- T5: The profile is cooled and then artificially aged, increasing its strength.
- T6: The profile is solution heat-treated, quenched, and then artificially aged to provide maximum strength.
E.O.T Cranes:
- 6 Heavy Duty EOT Cranes from 1 Ton to 10 Ton capacity.
Power Backup:
- Independent Feeder line for uninterrupted Power Supply.
- Multiple Generator of different capacity for running auxiliary load.
4 Fork Lift:
- One electric and three fork lifts running on diesel with a capacity of 3 ton to 5 tons.
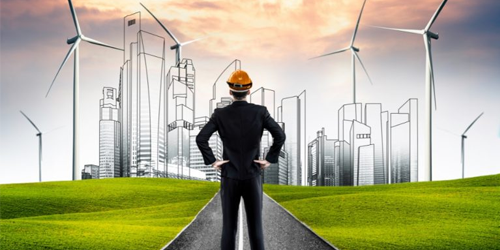
Green Fuel:
- Our generators and furnaces run on PNG, a GREEN FUEL, to reduce carbon footprint in keeping with our inherent responsibility towards the environment and has various anti-pollution control mechanism to reduce harmful emissions into the environment.
Health, safety and environment policy:
- We have the necessary equipments such as Solar Power Plant, Rain Water Harvesting, PNG based furnace and Generators, Wet scrubber, Recuperator ,E-Fork lifts etc to control the Air, Water and Noise pollution.
- Helmets, Shoes,Hand gloves, Respiratory Masks for staff safety.
- Spacious work place with abundant ventilation and exhaust system.
- Good drinking water by installing water-purifying machine.
- Clean and well maintained toilets/urinals.
- Adequate medical facilities.
- Protection from hazardous materials and conditions.
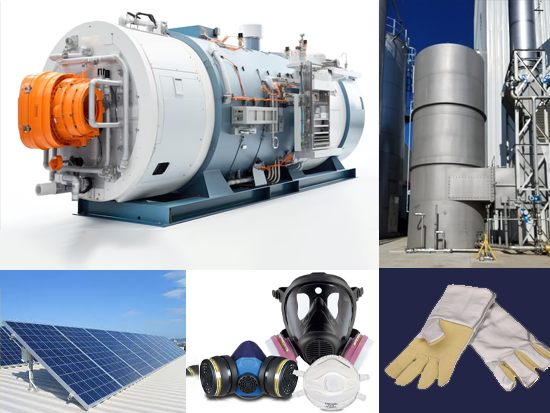