Aluminium’s unique properties make it an indispensable material for driving sustainability and innovation in a wide range of industries.
Aluminium future metal
Experience the future today with VRK Alumart Pvt. Ltd.
Why Aluminum is a Preferred Material?
Aluminum is a cost-effective and versatile metal used for an enormous number of environments and industries. Everything from household consumer products to advanced aerospace assemblies are made of aluminum. Aluminum also offers very high formability, making it easy and relatively inexpensive to shape, even into complex geometries.
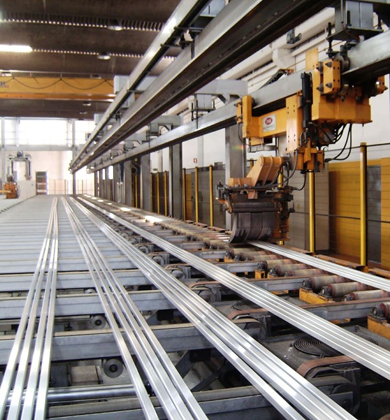
When the benefits of aluminum as a material are combined with forming through the extrusion process, the result is an unmatched combination of advantages:
- Strong, tough, and lightweight
- Corrosion resistant
- High thermal conductivity
- High electrical conductivity
- Cost and formability
- Accepts surface finishes
The Future of Aluminum Extrusion: Innovations and Breakthroughs Shaping the Industry
Aluminum extrusion has evolved significantly over the years, driven by technological advancements aimed at making the process more efficient, cost-effective, and capable of producing more complex designs. Recent innovations are poised to take aluminum extrusion even further, offering new ways to enhance product quality, reduce waste, and expand design possibilities. In this blog, we’ll explore some of the most exciting developments that are transforming aluminum extrusion and what they mean for the future of the industry.
-
Three-Dimensional Printing in Aluminum Extrusion
3D printing, or additive manufacturing, has already revolutionized many sectors, and its impact on aluminum extrusion is becoming increasingly apparent. Traditionally, extrusion dies are made through machining processes that can be time-consuming and expensive. However, 3D printing allows for the creation of complex and intricate dies at a fraction of the cost and time, making it easier to experiment with innovative designs.
By leveraging 3D printing for die production, manufacturers can achieve geometries and features that would be difficult or even impossible to create using traditional die-making methods. The ability to quickly and affordably prototype dies can lead to shorter lead times, reduced costs, and greater design flexibility. As 3D printing continues to evolve, its role in aluminum extrusion will only grow, offering exciting possibilities for the creation of lightweight, custom parts with optimized performance. -
Hot Extrusion: Enhanced Strength and Flexibility
Hot extrusion is a promising technology that involves extruding aluminum at higher temperatures than traditional methods. When aluminum is heated to higher temperatures, it becomes more pliable, allowing for the creation of thinner walls, finer details, and more complex shapes. This technique can also result in stronger aluminum components due to the grain structure alterations that occur at elevated temperatures, which enhance material strength and ductility. For industries such as aerospace, automotive, and construction, where strength-to-weight ratio is critical, hot extrusion opens up new possibilities for lightweight yet durable components. Additionally, by minimizing the need for additional post-processing steps, hot extrusion can improve efficiency and reduce manufacturing costs.
-
Synthetic Extrusion: Combining Additive and Subtractive Manufacturing
Synthetic extrusion is an emerging hybrid process that blends traditional extrusion with additive manufacturing (3D printing). In this process, a 3D-printed core is encapsulated by molten aluminum and extruded through a die. This combination of technologies allows for the creation of parts with intricate internal geometries that would be difficult to achieve through conventional extrusion alone.
One of the primary advantages of synthetic extrusion is its ability to produce components with enhanced design flexibility. Manufacturers can create structures with internal voids or complex channels, reducing material usage and improving the overall efficiency of the component. This technology is ideal for industries like aerospace and automotive, where complex parts with lightweight designs are often required. -
Nanostructured Aluminum: Stronger, Lighter, and More Durable
Nanotechnology is making waves across various industries, and aluminum extrusion is no exception. Nanostructured aluminum alloys, which incorporate nanoparticles into the aluminum matrix, offer improved mechanical properties such as enhanced strength, ductility, and fatigue resistance. These alloys enable the production of stronger, lighter, and more durable components.
In the context of aluminum extrusion, nanostructured aluminum offers the potential for creating more intricate and complex shapes without sacrificing strength or performance. These materials are particularly beneficial in high-performance applications like aerospace, automotive, and defense, where strength-to-weight ratio is paramount. Nanostructured aluminum can be extruded into high-precision parts that meet the most demanding requirements for quality and performance. -
Recycling Technologies: Boosting Efficiency and Sustainability
Aluminum is one of the most recyclable materials, and the aluminum extrusion industry is increasingly focusing on improving recycling processes. Recent advancements in recycling technologies are making it easier to recycle aluminum more efficiently, ensuring that the material can be reused without compromising its quality.
One such innovation is the use of microwave energy for sorting and separating aluminum scrap. This technology allows different aluminum alloys to be separated more effectively, reducing the need for manual sorting and improving the quality of recycled aluminum. By making aluminum recycling more efficient, manufacturers can reduce material costs, decrease environmental impact, and support sustainable production practices. As the demand for eco-friendly materials increases, recycling technologies will play an even more vital role in the future of aluminum extrusion. -
Artificial Intelligence: Optimizing the Extrusion Process
Artificial intelligence (AI) is transforming many industries, and aluminum extrusion is no exception. AI can be used to optimize various aspects of the extrusion process, from material selection to die design and process parameters. By leveraging machine learning algorithms, AI systems can predict and adjust process variables in real time, ensuring optimal performance and minimizing defects.
AI also plays a crucial role in quality control by enabling automated defect detection and real-time monitoring of the extrusion process. By identifying potential flaws in extruded components before they reach the end of the production line, AI can significantly reduce waste and improve product quality. Moreover, AI can predict maintenance needs for extrusion equipment, reducing downtime and extending the life of machinery. -
Robotics: Streamlining Automation and Enhancing Efficiency
The use of robotics in aluminum extrusion is another promising development that is helping to streamline operations and increase productivity. Robots are already being used to automate repetitive tasks like material handling, die insertion, and part removal, which reduces the need for manual labor and lowers the risk of human error. Robotics can also enhance quality control by performing precise inspections and measurements throughout the extrusion process. Automated systems can detect issues such as dimensional inaccuracies or surface defects, ensuring that only high-quality products are produced. Additionally, robots can operate around the clock, increasing throughput and reducing lead times.
The future of aluminum extrusion is brimming with exciting
possibilities thanks to the rapid pace of technological
advancements. Innovations such as 3D printing for die-making, hot
extrusion for enhanced material properties, synthetic extrusion for
more intricate designs, and AI-powered optimization are transforming
the industry and making aluminum extrusion more efficient,
sustainable, and adaptable.
By embracing these new technologies, manufacturers can produce
aluminum components that are stronger, lighter, and more complex
than ever before. The ability to recycle aluminum more efficiently,
combined with advanced robotics and AI-driven processes, will not
only enhance productivity but also reduce waste and environmental
impact.
As the industry continues to evolve, it’s clear that the future of
aluminum extrusion is about more than just manufacturing; it’s about
creating smarter, more sustainable solutions that meet the needs of
a rapidly changing world.
What does the futurehold for Aluminium Extrusion?
A Surge in Sustainable Practices
Recycling aluminium requires only 5% of the energy needed to produce new aluminium from raw ore. This remarkable efficiency makes it a key material in the circular economy, where resources are reused and recycled to minimise waste. In the next few years, we can anticipate more sophisticated recycling methods and closed-loop systems, ensuring that aluminium products are continuously repurposed.
Integration with Smart Manufacturing
The future of aluminium extrusion is closely tied to the rise of Industry 4.0 and smart manufacturing technologies. The integration of the Internet of Things (IoT), artificial intelligence (AI), and machine learning into the extrusion process will revolutionise production. Smart sensors and real-time data analytics will enable manufacturers to monitor and optimise every aspect of the extrusion process, from die design to product finishing. Predictive maintenance, enabled by AI, will reduce downtime and increase efficiency by anticipating equipment failures before they occur.
Expanding Applications in Emerging Industries
The energy sector, for example, will benefit from aluminium extrusions in the development of solar panels, wind turbines, and energy-efficient building materials.The growing field of electric vehicles (EVs) presents significant opportunities for aluminium extrusion. EV manufacturers are increasingly turning to aluminium to reduce vehicle weight and enhance energy efficiency.The flexibility and customisation capabilities of aluminium extrusion will allow manufacturers to meet the evolving demands of many sectors, from automotive and aerospace to construction and renewable energy.
Customisation and Flexibility
Advancements in extrusion technology will allow for the production of more complex shapes and profiles, expanding the possibilities for customisation. The combination of flexibility and precision will enable manufacturers to cater to niche markets and specialised applications, driving further growth in the industry.
Advanced Alloys for Improved Performance
The development of advance and high-strength aluminium alloys will also facilitate more complex and intricate extrusions, enabling manufacturers to produce components with enhanced performance characteristics. This evolution will open up new opportunities for design and functionality in many sectors.