Our Process
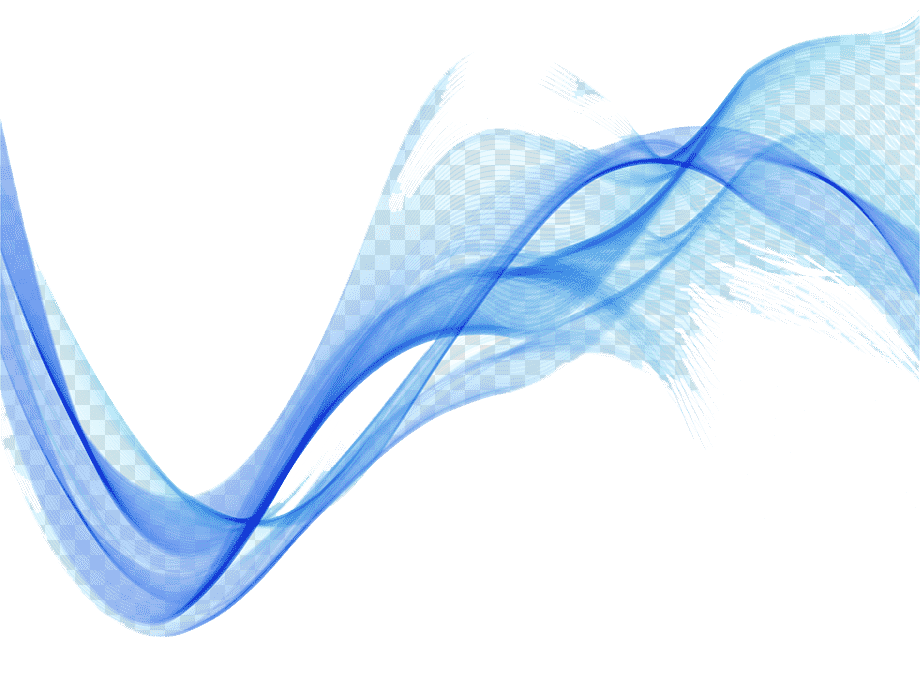
__ || NURTURING POTENTIAL, FUELING GROWTH || __
The extrusion process is a highly efficient, cost-effective, and versatile manufacturing method that enables the production of complex, high-precision extruded products with exceptional consistency. During the extrusion process, aluminum alloy is forced through a die, resulting in custom shapes with precise dimensions, making it ideal for various industries requiring durable and lightweight materials. The core of our success is built on a combination of state-of-the-art indigenous manufacturing units, an unwavering commitment to innovation, rigorous onsite testing, strict quality checks, and a strong dedication to environmental sustainability at every stage of production.
The extrusion process allows for the production of three primary types of shapes, each suited for different applications
Semi-Hollow Shapes
These profiles have partially enclosed voids, offering a balance between material efficiency and structural strength. Semi-hollow extrusions are ideal when partial internal cavities are needed for specific mechanical properties, such as flexibility, weight reduction, or thermal performance
Extrusion Process
-
Step 1: Obtaining and Handling Aluminum Scrap:
The company boasts a robust global sourcing
network, ensuring a consistent supply of high-quality
aluminum scrap, including wire scrap, Taint Tabour (TT),
sections (6063, 6061, 6082), and primary aluminum ingots
from both international markets and local suppliers, as well
as primary ingot manufacturers.With a minimum procurement
volume of 1,600 MT per month (or 20,000 MT annually), the
company maintains a stable and reliable supply chain,
ensuring seamless production operations.
- Raw Material Testing: All aluminum scrap materials are subjected to ultrasonic testing to ensure that the material is free of impurities, which is crucial for maintaining the integrity of the final product.
- Processing and Segregation: Once sourced, the aluminum scrap is processed and segregated using advanced technologies which helps to remove most impurities, making the scrap ready for use in furnaces.By effectively segregating and refining the scrap, the company ensures the consistency, strength, and performance of the final extruded products.
-
Step 2: Production of Alloys & Logs in Melting Furnaces
Once the aluminum scrap or primary aluminum has been procured and
inspected, it is subjected to the melting process to produce alloys.
- Melting the Aluminum Raw Materials: The selected aluminum raw materials are loaded into melting furnaces, where they are heated to reach a liquid state to form the base of the alloy. The temperature is carefully controlled to ensure the metal reaches the correct viscosity for alloying.
- Alloying Elements Addition: To create the specific aluminum alloys required, additional elements are added to the molten aluminum. These may include: Magnesium, Silicon, Manganese, Strontium, Titanium, Copper, Zincbased on the desired properties of the final product, such as strength, hardness, or corrosion resistance.
- Molten Metal Treatment: Before casting the molten metal into logs, it undergoes treatment to remove unwanted impurities, such as inclusions and hydrogen. The treatment process may involve degassing or filtering to remove these contaminants.
- Casting into Logs Once the molten metal is properly alloyed and treated, a sample at that stage first is subjected to an automated examination using state-of-the-art spectrometer technology and then the treated molten metal is poured into log-shaped molds to form large ingots. The casting process is done using a ceramic double filtration system that helps filter the molten metal as it is poured, ensuring that any remaining impurities are removed, and the alloy maintains high quality
- Spectrometer Examination The company uses a German-made Spectro Analytical Instrument for precise and accurate analysis of the metal’s composition. This helps ensure that the alloy meets stringent quality standards.
-
Step 3: Checking the Quality of Logs:
After the aluminum logs are cast and solidified, they undergo a
thorough quality check to ensure that they meet the required
standards before moving on to the next stage of the manufacturing
process
- Visual Inspection for Defects such as cracks, holes and other imperfections, Logs with any of these defects are typically rejected or sent for further processing to remove or correct the issues.
- Dimensional Accuracy inspection which include lenth,diameter/width to ensure that they conform to the required specifications for the extrusion process.
- Chemical Composition Testing using spectrometer analysis to ensure that the material has the desired chemical elements such as Manganese (Mn),Iron (Fe),Magnesium (Mg),Silicon (Si),Zinc (Zn),Titanium (Ti),Chromium (Cr),Copper (Cu),Aluminum (Al).
- Ensuring Final Product Quality so that the material can be safely and efficiently processed into high-quality extrusions without issues.
-
Step 4: Die Preparation
Once the aluminum scrap or primary aluminum has been procured and
inspected, it is subjected to the melting process to produce alloys.
- Die Design and Machining The extrusion die is typically made from high-strength steel, which is carefully machined to match the precise cross-sectional profile of the product to be created.
- Preheating the Die Before the extrusion process begins, the die must be preheated to temperatures between 450°C and 500°C for Smooth Metal Flow, Reduced Risk of Uneven Flow and for Extended Die Life by reducing the thermal shock that occurs when hot aluminum meets a cold die. This minimizes wear and tear on the die, making it more durable and reducing maintenance costs.
- Die Maintenance As part of the die preparation, regular maintenance is also performed to ensure the die remains in optimal condition. This includes checking for any wear or damage to the die and performing any necessary repairsfor producing high-quality aluminum profiles with the required accuracy and surface finish.
-
Step 5: Billet Preheating
After the aluminum logs are cast and solidified, they undergo a
thorough quality check to ensure that they meet the required
standards before moving on to the next stage of the manufacturing
process
- Billet Cutting The first part of this step involves cutting aluminum billets from the longer aluminum logs. The billets are cut to precise lengths to match the needs of the extrusion press.
- Preheating the Billets Once the billets are cut, they are then preheatedin industrial ovens to a temperature range of 400-500°Cby ensuring that the billets are neither under-heated nor over-heated.This step is significant to Increase Malleability, for Smooth Flow Through the Die and to Avoid Melting. The temperature is carefully controlled to ensure that the aluminum stays solid but becomes soft enough for the extrusion process.
-
Step 6: Extrusion Process
The extrusion process is where the heated aluminum billet is
transformed into a continuous profile with a specific
cross-sectional shape, using a powerful hydraulic press.
- Billet Transfer to the Extrusion Press
- Application of Pressure by The hydraulic ram which applies up to 15,000 tons of pressure to the heated billet. This immense force is required to push the malleable aluminum through the preheated die
- Heated billet Flow Through the Die - The material flows continuously, emerging from the die as an elongated profile of aluminum from simple shapes like bars or rods to more complex forms, like window frames, pipes, or custom components.
- Precision Control- The precision of the die and the control of pressure are key factors in ensuring that the final shape of the aluminum profile matches the specifications exactly. In addition to these, the temperature and speed of extrusion must be precisely monitored to ensure the right balance of strength, formability, and surface quality.
-
Step 7: Quenching
After exiting the die,to solidify the shape and lock in the
mechanical properties, the extruded profile undergoes quenching—a
rapid cooling process that helps set its structure and hardness,
which ensures the newly formed aluminum profile retains the desired
mechanical properties. It is essential to achieve uniform cooling
across the entire profile to prevent distortion or warping. This
cooling can be done using water baths or air fans, depending on the
alloy and the required properties of the finished product.
- The cooling rate directly impacts the microstructure of the aluminum, which in turn affects properties like tensile strength, durability, and corrosion resistance.
- The quenching process also plays a role in determining the workability of the material, making it easier to handle and process in subsequent steps.
-
Step 8: Shearing and Cooling
After the aluminum profile has been extruded and quenched, it
undergoes the final steps of shearing and cooling to achieve the
required length and ensure the material has fully solidified.
- Shearing to Table Length Once the extruded aluminum reaches its full length on the runout table (the conveyor or track that moves the profiles after extrusion), it is ready to be cut to the required length using a hot saw to cut the aluminum profiles.This length is typically predetermined to ensure the profiles can be easily handled, stored, or transported.
- Further Cooling on the Cooling Table While the extrusion has been quenched to reduce its temperature and harden the material, it has not fully cooled down to room temperature. Therefore the aluminum profiles are transferred to a cooling tablefor a set period. During this time, they may be subjected to air cooling, where fans or ambient airflow help dissipate the remaining heat.
-
Step 9: Stretching and Alignment
During the cooling process, natural twisting or bending may occur in
the aluminum profiles.
To correct this, the extrusions are transferred to a stretcher, where they are mechanically pulled from both ends to ensure they are perfectly straight and aligned to the required specificationsto achieve dimensional accuracy.
-
Step 11: Aging
The aging process is essential for achieving the desired strength
and hardness in the aluminum profiles, making it a key step in
ensuring the final product performs well under stress, is durable,
and meets the specific requirements of its application.
- Heating: The aluminum profiles are heated to around 180°C in an aging furnace.
- Holding The profiles are held at this temperature for 4-5 hours to allow precipitation hardening, which enhances strength and hardness.
- Cooling After aging, the profiles are allowed to cool back to room temperature, completing the aging process.After sufficient aging, whether in an aging oven or at room temperature, the profiles are moved to other areas of the plant and may be finished (painted or anodized), fabricated (cut, machined, bent, welded, assembled), or packed for shipment.
The Role of Temperature, Pressure,
and
Precision in
Aluminium Extrusion
- The extrusion process relies heavily on controlling temperature and pressure.
- This balance of heat and pressure ensures the final product is strong, precise, and suited for its intended application.
Temperature
The temperature of the aluminum billet is crucial for achieving high-quality extrusion results.
- Role: Billets are heated to between 400-500°C to make the aluminum malleable but not molten. The right temperature allows for smooth extrusion without compromising the strength of the material.
- Impact: If the temperature is too high, the aluminum can become too soft, leading to poor dimensional accuracy and surface finish. Too low, and the billet may crack or resist proper extrusion.
Pressure
Pressure plays a central role in pushing the aluminum billet through the die to create the desired shape.
- Role: Hydraulic rams apply immense pressure (up to 15,000 tons) to force the aluminum through the die.
- Impact: Insufficient pressure can result in incomplete filling of the die or inconsistent profiles, while excessive pressure can cause defects or damage to the extrusion equipment.
Extrusion Speed
The speed at which the aluminum is extruded needs to be carefully controlled to ensure uniformity.
- Role: Faster speeds can increase productivity but can also lead to overheating and surface defects. Slower speeds offer better control but can prolong the process.
- Impact: Balancing speed with temperature and pressure ensures that the extrusion process produces profiles with consistent dimensions and properties.
Extrusion Ratio
The extrusion ratio refers to the relationship between the cross-sectional area of the billet and the final extruded shape.
- Role: A higher extrusion ratio means the billet must be compressed more, which can result in greater strength and better mechanical properties.
- Impact: Lower extrusion ratios may result in products with less mechanical work, leading to a weaker profile. Higher ratios require more pressure and energy but often yield stronger, more durable parts.