Quality & Testing
__ || COMMITTED TO QUALITY, Delivery WITH PRIDE || __
Quality & Testing
At VRK Alumart Pvt. Ltd., Quality is the utmost priority. We firmly believe that consistent product quality is crucial in shaping the overall customer experience, driving higher satisfaction, fostering increased loyalty, and generating positive word-of-mouth referrals. To ensure this consistency, VRK Alumart invests heavily in state-of- the-art tools and machinery, efficient processes, and cutting-edge quality control solutions designed to meet compliance standards.
Our company is committed to streamlining manufacturing operations, enhancing collaboration with suppliers, and leveraging analytics and reporting to continuously improve product quality. By maintaining this level of consistency, we minimize defects, reduce waste, and prevent costly reworks, which ultimately leads to better resource utilization and operational efficiency.
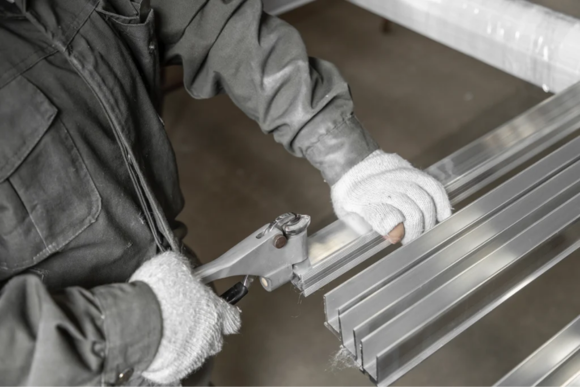
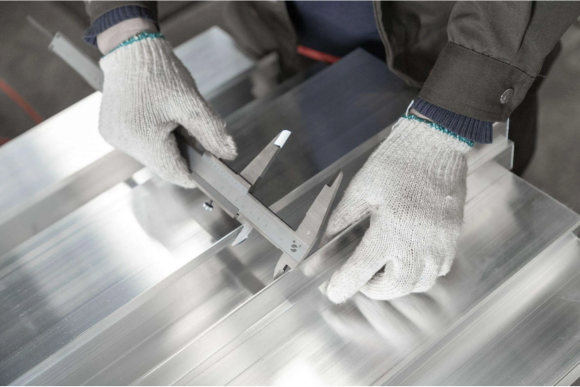
In addition, VRK Alumart takes proactive steps by implementing
regular inspections and audits throughout the production process.
These quality control measures help identify and address potential
issues early, reducing the chances of producing substandard
products. This early detection enables the more efficient use of
materials and labor, resulting in both cost savings and improved
product output.Our focus on quality is further supported by our
rigorous process control systems, a state-of-the-art Quality Lab, and
a team of expert professionals who work tirelessly to ensure the
quality of both incoming raw materials and finished products. Every
stage of production is meticulously scrutinized to guarantee the final
product meets the highest standards.
VRK Alumart not only ensures product consistency but also sets the
foundation for achieving long-term success in the global market. Our
unwavering commitment to quality is a key driver of our reputation
and positions us as a leader in the aluminum extrusion industry.
Quality Control Methods for Aluminum Extrusion at VRK Alumart Pvt. Ltd.
At VRK Alumart Pvt. Ltd., we implement a comprehensive set of quality control methods to ensure the highest standards in aluminum extrusion. These measures are applied at every stage of the process, from procuring raw materials to post-extrusion inspection, ensuring that our products meet the desired specifications and industry standards.
Procurement and Processing of Aluminum Scrap
- Raw Material Examination: We begin with ultrasonically examining raw materials for hydrogen content and grain structure, ensuring that the aluminum scrap meets the necessary standards before being processed.
- Scrap Segregation: Using advanced technologies, we are fully equipped to process and segregate a wide range of scrap types, ensuring that the materials fed into the furnaces are mostly free of impurities.
Examination of Alloys
- At VRK Alumart Pvt. Ltd., we understand that the quality of the aluminum alloy is foundational to the final product’s performance and integrity. Our process for alloy examination is rigorous, ensuring that each batch meets the highest standards before it enters the extrusion phase.
- By combining clean melting processes, state-of-the-art spectrometer technology, and advanced casting techniques, VRK Alumart ensures that every batch of aluminum alloy meets stringent quality standards. This comprehensive approach guarantees that our alloys are free from impurities, have the right chemical composition, and possess the necessary mechanical properties to perform optimally in the extrusion process, resulting in high-quality profiles with excellent strength, durability, and appearance.
Control of Billet Quality
- Each billet is thoroughly tested to ensure its chemical composition aligns with the specific alloy standards required for the extrusion process
- We rigorously check the mechanical properties of billets, such as strength and ductility, to ensure they meet the necessary performance criteria for the intended application.
- Billets are carefully examined for surface defects such as cracks, cavities, and inclusions. These imperfections can significantly impact the quality of the extruded product, leading to defects that compromise the final product's appearance, structural integrity, or functionality.
Die Design and Maintenance
- By carefully controlling the die geometry and flow patterns, we reduce the risk of imperfections like streaks, roughness, and other surface defects that could affect the final product's appearance. Our dies are engineered to maintain the correct profile dimensions and minimize distortions such as warping or bending, which can occur during extrusion. Additionally, we maintain our dies to prevent wear and strain that could affect product quality.
In-line Quality Checks
- As the extrusion process is ongoing, automated systems continuously measure critical parameters like dimensional accuracy, shape consistency, and surface quality.
- Our technologies provide a detailed analysis of the profile's surface, allowing for immediate corrective action if any defects are detected.
- We keep a check that the extruded profiles meet the required dimensions, ensuring that they conform to customer specifications. This includes measurements of width, thickness, length, and any other critical profile features.
- If a non-conforming profile is detected, the system immediately flags it for further inspection or removal from the production line.
- By identifying defects early, in-line quality checks reduce the amount of scrap material and prevent further processing of faulty products. This contributes to cost savings and ensures that only products meeting the highest standards are delivered to customers.
Extrusion Process Control
- Process Parameter Monitoring: We continuously monitor and manage the extrusion process parameters, such as temperature, speed, and pressure, to ensure they remain within the defined range. Any deviation from the established criteria could result in defects like surface finish flaws, shape distortion, or internal voids, so maintaining consistent process control is essential.
Comprehensive Post-Extrusion Quality Assessment
- After extrusion, a thorough inspection is conducted to verify the profiles' dimensional accuracy, surface finish, mechanical properties, and any other specific customer requirements. We employ techniques like coordinate measuring machines (CMMs), visual inspection, and mechanical testing to ensure the profiles meet the highest standards.
Quality Check at the Packaging Stage
- Proper packaging ensures that the finished products reach our customers in optimal condition, free from damage or defects that may arise during handling or transportation.
- To avoid damage during transit, the extruded profiles are carefully packaged using protective materials, such as foam padding, corner protectors, or stretch film.
- Each package is labeled with clear and accurate information, including details about the material grade, customer order, and batch number for traceability.
- The quantity and weight of the packaged products are double- checked against the customer’s order specifications to ensure that the correct amount of product is being delivered.
Quality Documentation and Traceability
- Documentation for Accountability: Detailed and accurate quality documentation is maintained for every step of the process, including raw material inspection, process monitoring, in-line checks, and post-extrusion inspection. This ensures traceability and accountability in aluminum extrusion manufacturing, providing a complete quality history for each product. This traceability is vital for addressing any quality- related issues promptly and serves as a reference for continuous improvement initiatives.